As you already know, your engine’s combustion process involves mixing air and fuel. What you might not know is that managing air is significantly more difficult than managing fuel. This has to do with air being more reactive to humidity and temperature than fuel is. On top of all of this, air can behave extremely weird when under pressure and vacuum. That being said, having the right air suspension management system is essential to the performance of your vehicle.
The engine control unit (ECU) has to change the open timer of the injector and regulate the rail pressure with fuel. Controlling the air, however, is much more complicated. Fortunately, with direct injection, modern vehicles have become significantly better at delivering the right amount of air, at the correct time. Let’s go in-depth about the air suspension management processes, and how they impact your vehicle.
Throttle Control
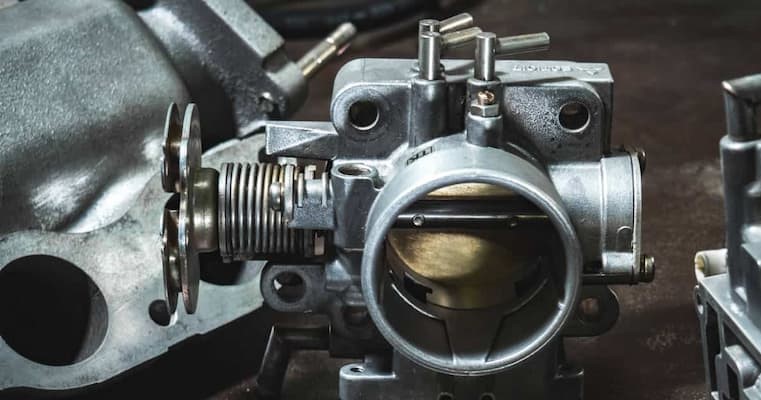
Before the air gets into the combustion chamber, it has to go through the throttle plate and intake valves. The management of these openings is essential to the performance and fuel economy of your vehicle. In older cable-operated throttle systems, where the gas pedal mechanically pulled the throttle cable, the engine control unit had to fight off the immediate throttle angle by injecting more fuel and changing the ignition. As a result, you didn’t get the right ratio of fuel and air.
The throttle plate is responsible for letting enough air get into the engine. With throttle-by-wire systems, the amount of throttle commanded by the pedal never matched the percentage of the throttle opening at the butterfly. Even when idling, the throttle angle is constantly shifting. When you press the pedal to the floor, the throttle opens so the air can match the fuel, engine load and speed. However, the throttle plate is just the first checkpoint air passes through.
Ports and Runners
Between the throttle plate and intake valves is the intake manifold. Modern manifolds have two ways to control airflow. The variable intake runners adjust the length of the intake passage based on engine load and speed. Generally, longer runners produce more torque at low-end engine speeds. Shorter runners, on the other hand, produce more power at high-end engine speeds.
There are also valves positioned at the end of the intake runners before the intake valves. These valves are in charge of controlling the shape and size of the intake port. Moreover, they help create a manifold that’s the proper size for the engine’s demands. The valves assist in swirling or tumbling air to reduce turbulence as the air enters the cylinder. They close down the ports at low engine speeds and open completely as your vehicle speeds and the load increases.
Different manufacturers name their valve systems differently. Volkswagen calls it the Variable Tumble System, whereas Hyundai calls it the Variable Charge Motion Actuator.
When the valves stop working, they can fail in the closed or opened position. When they fail in a closed position, the engine can starve for air and act become sluggish. If stuck in the open position, the engine can have poor idle quality and stumble when accelerating. Generally, these systems come with position sensors that trigger codes when they see actuators not moving or moving at a slower rate. Some failures can result in misfires and fuel trims that can be too rich or too lean
Variable Valve Timing
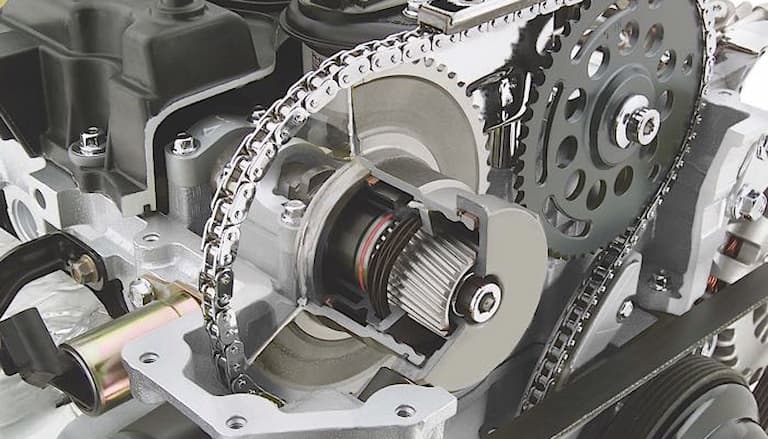
At lower speeds, variable valve systems on the intake camshaft open the valves later during the stroke. This, in turn, increases the vacuum and scavenging capabilities generated by the piston as it goes downward on the cylinder. As a result, you get improved idle quality and smoother power tip-in. As the RPMs in the engine increase, the intake valves open faster. Ultimately, this enhances torque.
At higher speeds, the valve open later for full-on power delivery, allowing the scavenging effect of the exhaust to leave the cylinder to pull more air. The fly-by-wire system helps optimise the scavenging capabilities and allows just enough air into the cylinder.
How it All Adds Up
The aforementioned parts work together in unison to manage the air that goes into the cylinders. If something goes wrong in any of those parts, it can negatively impact the performance of the rest, and ultimately, negatively impact what happens inside the combustion chamber, and what the oxygen sensor detects in the exhaust gases.
If air management system parts fail without notice, many technicians will only look at the ignition and fuel parts, simply because they’re easier to understand and see than air. Troubleshooting an issue that involves the air management parts of a vehicle requires proper repair information and specialised tools. A scan tool that can check the operation and position of the actuators can provide access to data PIDS. Moreover, bi-directional controls to motors and manually actuating solenoids can confirm their working condition. However, the most important tools for inspecting the whole system are your eyes.